R-300 – AUV/ROV
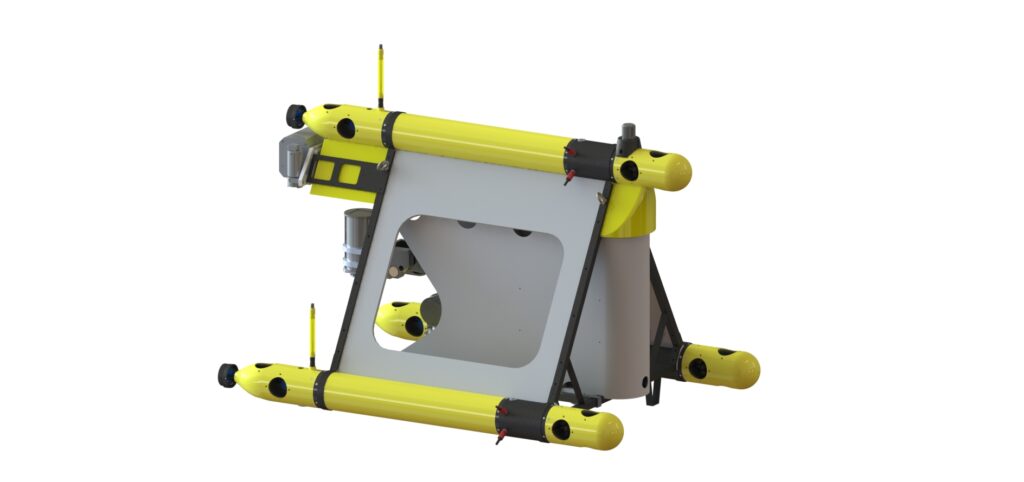
product
Specifications
-
Lenght:
2044 mm
-
Weight in air:
180 kg
-
Playload capability:
60 kg
-
Speed:
4 knots
-
Energy Storage:
Li-Ion Batteries 14,4 Volt – 3200 Wh (expandible)
-
Endurance:
12 hours at max speed
-
Navigation sensors:
GPS, depth-meter, 3D inclinometer, INS
-
Software:
Windows GUI
-
Communication:
WiFi radio Link (Short range 1km), Optical fiber (if requested)
introduction
What is R-300
R-300 is the ROBUST vehicle of the X-300 family, designed for carrying bulky and heavy payloads. It is constituted by three short X-300 AUVs which are attached to a triangular aluminium frame supporting the installation of many different equipment of interest. A connection module mounted at the bow of each X-300 provides a common power and data link among the three composing AUVs and enables their effective motion coordination. As a result, R-300 is an extremely agile vehicle with high maneuvrability, that can operate either as a standard AUV, or as a ROV thanks to the available fiber-optic tether.
High payload capabilities
The presence of the connecting frame allows to install on-board the vehicle a relevant number of different instruments and tools, including bulky devices that otherwise could not be carried by a standard torpedo shaped X-300. As an example, R-300 can host a 7-axis manipulator, like UMA 1500, that can be used for rescue missions or for maintenance activities on offshore installations. At the same time, together with the robotic arm, R-300 can transport also acquisition sensors (like sonars and cameras) and navigation devices (like DVL and IMU) with the required additional processing units. Finally, whenever a longer endurance is required, additional batteries can be easily added to the frame.
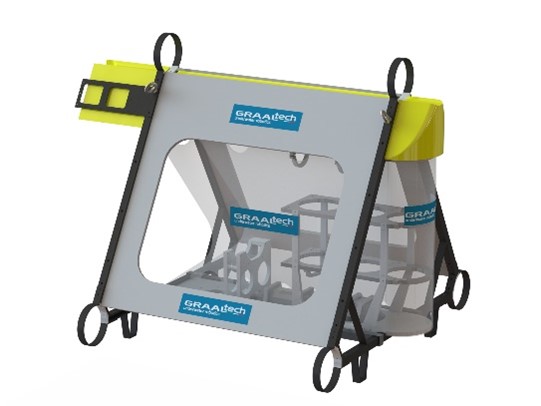
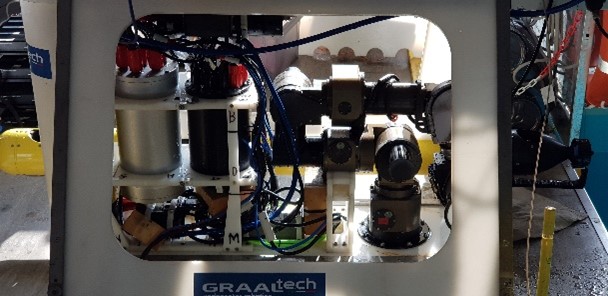
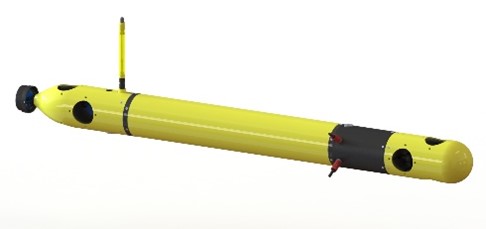
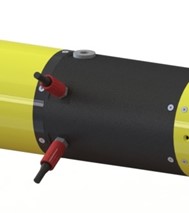
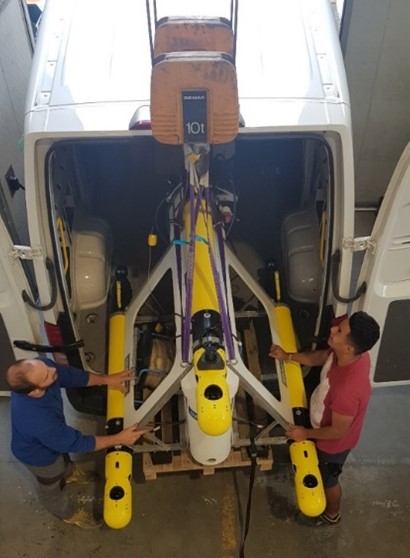
Short X-300 with connection module
Every composing X-300 has a short configuration, obtained by replacing the front cylinder containing the variable buoyancy system with a small connection module with up to six underwater connectors available. Two of them are always used for interfacing each X-300 with a centralized cylinder, providing a common power and data line. The other four are free and can be employed for integrating additional equipment of interest.
The absence of the buoyancy chambers clearly prevents the navigation modes based on the active change of buoyancy (glider and profiler), but the resulting R-300 vehicle gains a lot in terms of weight and size, and becomes easier to transport, deploy and recover. In any case, whenever needed, a single variable buoyancy system can be installed on the vehicle frame and connected to one of the composing X-300, by exploiting one of the available spare connectors in the connection module.
High maneuvrability
The presence of three composing X-300 provides R-300 with a total number of 15 thrusters, that can be selectively tuned for doing hovering and for executing ROV-like motions along all the possible directions. R-300 can indeed move forward and backward, translate both vertically and horizontally, rotate on the spot and actively control the pitch and the roll.
In addition, R-300 can also land on the seabed or on a submerged installation and stay there for gathering measurements, taking samples or using its manipulator for performing maintenance activities on the underwater infrastructures.
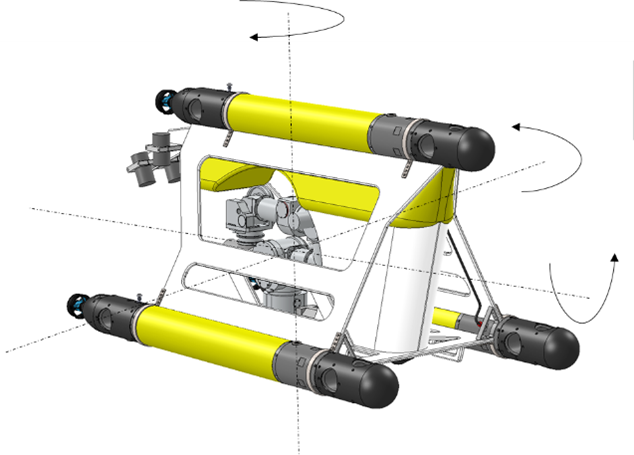
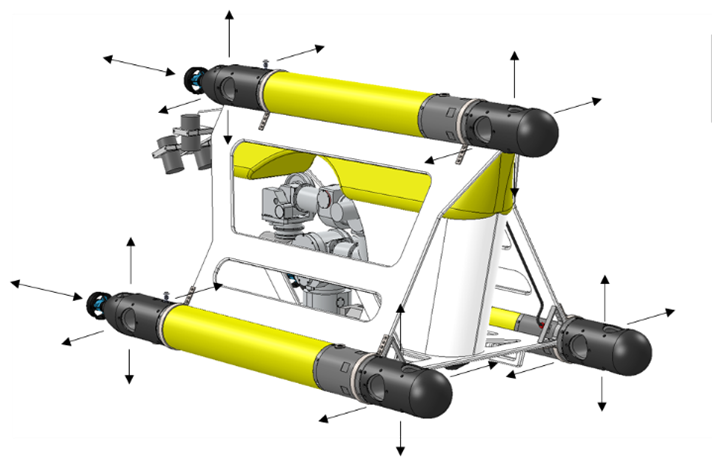
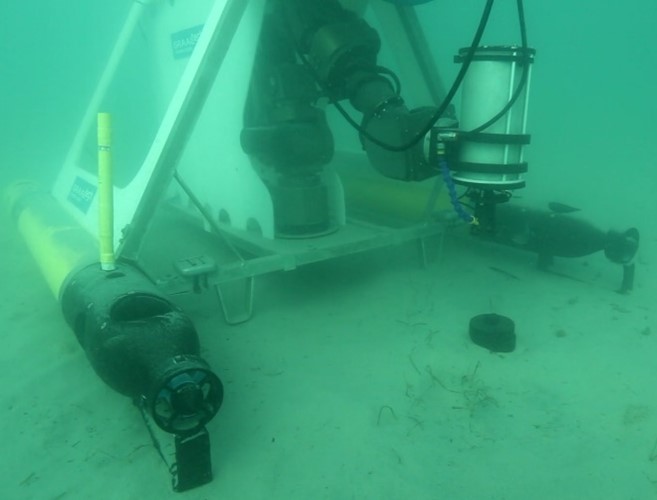
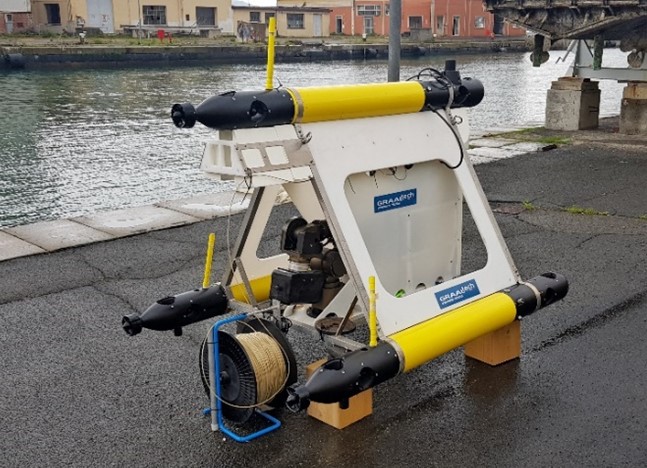
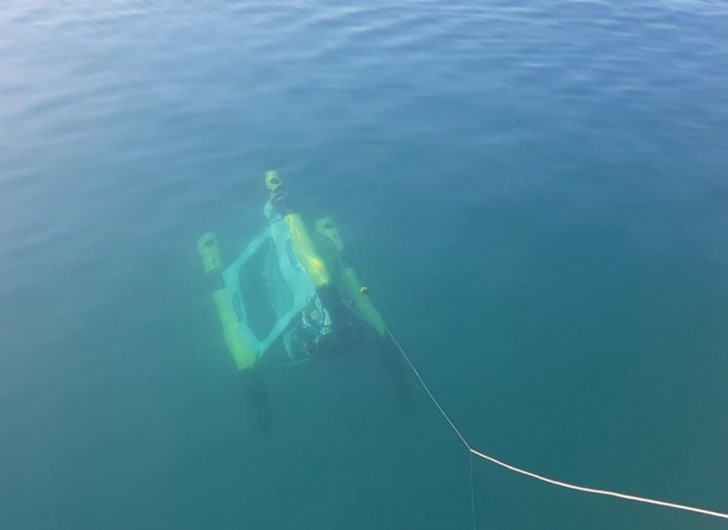
Fiber-optic Tether
R-300 can be delivered with a fiber-optic tether that allows a direct connection between the network hub of the vehicle and the control center on surface. In this way, not only the main CPUs of the three composing X-300 AUVs, but also all the transported devices with an Ethernet output, become directly accessible to the user during the underwater mission. The vehicle can still work in AUV mode for executing a pre-programmed mission. However, the user can monitor all the operations and, whenever desired, can stop the mission execution in autonomous mode, switching to manual control for remotely operating the vehicle. The ROV mode is in any case necessary when a robotic arm is installed, for piloting the manipulator when needed, as autonomous manipulation tasks are not currently foreseen. The tether can be delivered with different lengths, up to 5 km. For length above 1 km, the auxilium of a motorized wheel (available as an optional item) is recommended.